About us
Our goal is to assist you to develop innovative products and processes to build a sustainable and profitable biorefining industry in Australia. Our team engage in projects and consulting activities with industry as part of our everyday business.
We aim to increase the uptake of renewable bioproduct technologies, circular economy operations and distributed manufacturing in Australia by developing innovative, commercially viable products and processes.
We want to know your challenges so we can assemble the right team to move your project forward. To arrange a consultation, please contact brf@qut.edu.au
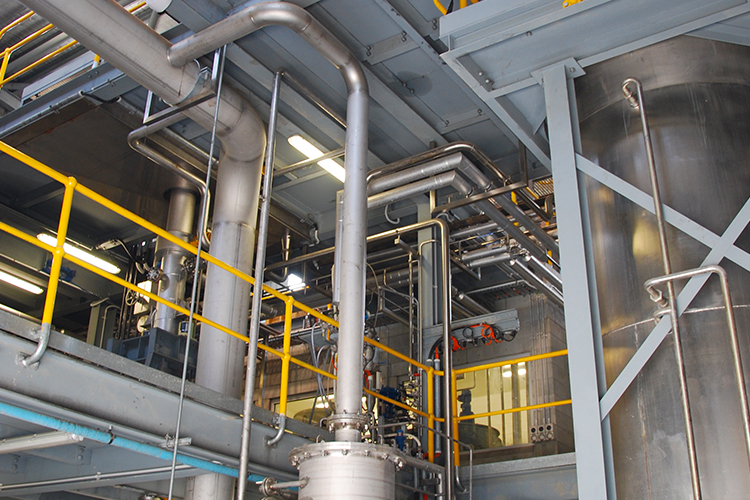
BRF is an arm of QUT’s Research Infrastructure (RI). We aim to assist researchers to develop innovative products and processes that enhance development of a sustainable and profitable biorefining industry in Australia. Our team engages in projects and consulting activities with academic and industry partners as part of our everyday business.
BRF has two primary locations:
- QUT - Fermentation and Bioprocessing Laboratory (PC2 with BC2 pending)
- Provision of laboratory scale bioprocessing equipment and expertise in precision fermentation and downstream processing.
- QUT - Mackay Renewable Biocommodities Pilot Plant - Research (PC1 & PC2 pending upgrade)
- Based on the site of an operating sugar mill, MRBPP enables pilot scale research and development in industrial biotechnology and biomass processing technologies and practices.
In addition, our staff also collaborate with other research facilities to achieve real-world outcomes for our partners e.g. QUT’s Banyo Pilot Plant and Central Analytical Research Facility.
Our facilities
Mackay Renewable Biocommodities Pilot Plant
Our Mackay Pilot Plant is pioneering research and innovation in biorefining.
The Pilot Plant is hosted by Mackay Sugar Limited, and is based on-site with an operating sugar factory, giving our researchers direct access to sugar, biomass and sugarcane co-products.
Access to raw materials and a dedicated, unique space means that our researchers can develop and demonstrate a range of technologies at pilot scale.
Fermentation and Bioprocessing Laboratory
BRF’s Brisbane Gardens Point Q620 PC2 biotechnology facility which has a range of equipment for bioprocessing research & development.
Capabilities
We assist you to develop products and processes for research, industry and government partners in the biorefining sector.
Biology and fermentation
We help create end-to-end fermentation processes from strain development through to fermentation optimisation and scale-up. Our expertise encompasses all stages of the fermentation process and can be segmented or scaled to suit project scope.
- strain development (genetically modified and non-genetically modified)
- screening and selection of fermentation strains
- feedstock selection and media optimisation
- 1L with scale up to 2,000L fermentations
- batch, fed-batch and continuous
- process monitoring, control and optimisation.
Materials/downstream processing
We have a range of laboratory and pilot scale materials processing equipment to modify industrial materials to suit your bioprocessing needs. From concentration, drying to separation of components of interest from complex mixtures our team have a broad range of expertise and equipment to assist your bioprocessing requirements.
- solid-liquid separation and concentration (e.g. centrifugation; TFF)
- evaporation
- clarification
- cell disruption and homogenisation
- distillation
- solvent extraction
- vacuum drying
- spray drying
- freeze drying.
Materials transformations
We operate thermal and chemical extraction equipment which may be utilised to transform a variety of materials from pre-processed materials through to agricultural biomass and other waste materials such as textiles and digestates. Components derived from these processes can be used to produce a broad range of products including liquid and gaseous fuels, and bioproducts used in flavours, organic acids, pharmaceuticals, phenolics, resins and plastics.
- horizontal reactor: provides the flexibility to perform a diverse range of pre-treatment technologies using various chemicals at moderate temperatures
- vertical reactor: materials are pressurised up to 24barG (up to 220oC) in the reactor by steam and flashed into a blow-down tank at atmospheric pressure by opening a fast-acting blow valve
- continuous hydrotreater: involves the application of hydrogen in the presence of a high activity catalyst at a suitable pressure (50-100 bar) and temperature to transform materials
- Pparr high temperature and pressure batch reactors: 5, 7 and 20L capacities
- continuous hydrothermal liquefaction (HTL) reactor: 10lph 250 bar operating conditions
- REACH process pilot plant
- extrusion – equipment details to be confirmed as part of MRBPP upgrade
- Sanflo Mill.