Greener alternatives from biorefining
Our Mackay Pilot Plant is pioneering research and innovation in biorefining. By turning agricultural biomass into cleaner bioproducts, we’re supporting an increased uptake of renewable processes and creating a more profitable and sustainable agriculture sector.
Our researchers are creating biofuels, green chemicals and other bioproducts using biomass feedstocks such as sugarcane bagasse, trash and molasses, as well as and other agricultural products like cotton, grains and horticultural wastes. We’re developing the innovative and clean products and processes integral to a greener future.
Working on-site with industry
Our Mackay Pilot Plant is pioneering research and innovation in biorefining. By turning agricultural carbon sources such as sugars and biomass into cleaner bioproducts, we’re supporting an increased uptake of renewable processes and creating a more profitable and sustainable agriculture sector.
Our researchers are creating future foods, biofuels, green chemicals and other bioproducts using sugarcane based feedstocks, as well as and other agricultural products like cotton, grains and horticultural wastes. We’re developing the innovative and clean products and processes integral to a greener future.
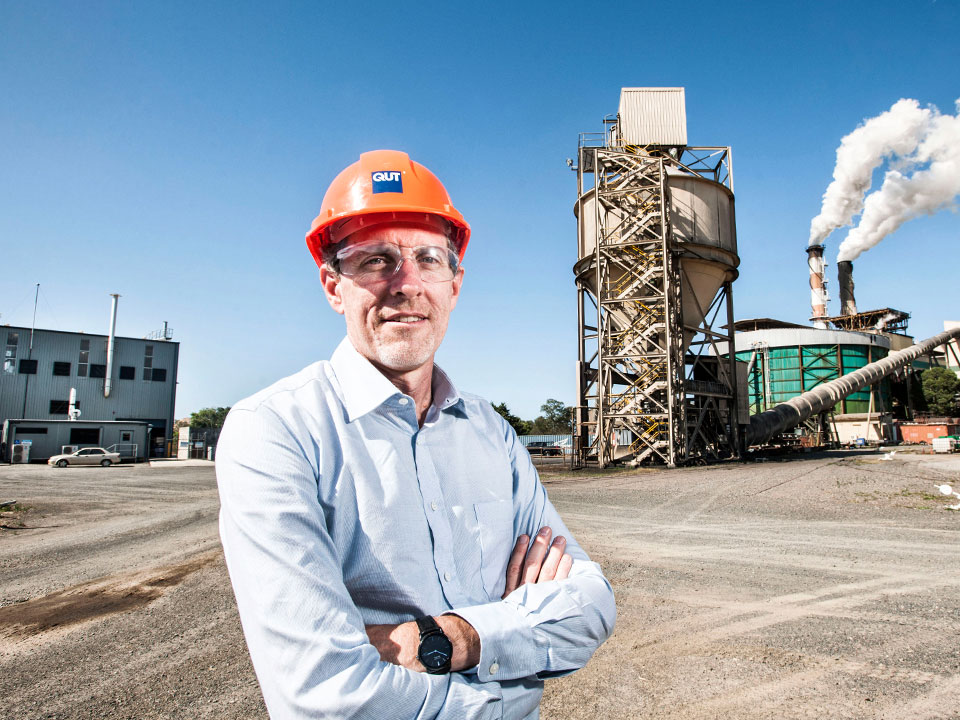
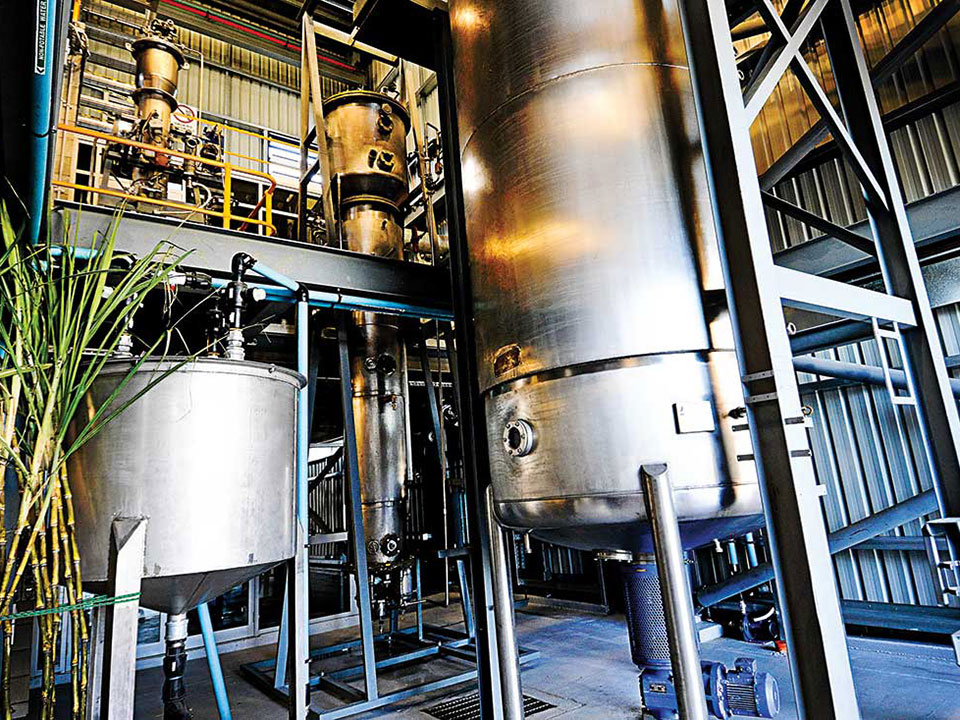
Finding a sustainable future
The Mackay Pilot Plant is part of our Centre for Agriculture and the Bioeconomy - a research centre dedicated to developing a sustainable future through biotechnology and bioproducts.
We make the most of this expertise, in combination with the Pilot Plant's unique infrastructure, to build capacity in renewable production.
Equipment
MRBPP equipment may be grouped into two broad categories:
- Pre-treatment and thermochemical transformation
- PC2 large scale precision fermentation and downstream processing (food grade)
Pre-treatment and thermochemical transformation
Equipment | Features |
---|---|
Horizontal reactor – pre-hydrolysis process Materials are mixed with chemicals and steam to break them up and make them easier to digest. The crystallinity of cellulose is reduced, and the porosity is increased in the process. |
Up to 4 batches per day capacity |
Vertical reactor – steam explosion In this reactor, materials are pressurised up to 24barG temperature up to 220oC) in the reactor by steam and flashed into a blow-down tank at atmospheric pressure by opening a fast-acting blow valve. This elevated temperature and fast decompression process can cause bursting of cellular tissue and weaken the links between fibrous components. |
Up to 50 litres of material per batch |
Cutting mill Retsch SM300 Dried materials are cut and grinded down through mechanical shredding processes to reduce the particle size. It is specially designed for the grinding of soft, medium-hard, tough, elastic, fibrous, and heterogeneous mixes of products. |
|
Chipper/mulcher This garden shredder / chipper / mulcher reduces the size of biomass feedstocks. Biomass can include, and is not limited to, sugarcane, bagasse, trash, corn stover, wood chip and energy grasses. |
A 3.5" (89mm) chipping capacity in the side chipper hopper and 25mm shredding capacity in the top big hopper for easy feeding of bushy branches with less preparation |
REACH pilot plant REnewable Acid-hydrolysis Condensation and Hydrotreating Thermochemical transformation converts biomass and waste feedstock into biocrude oil, syngas, solid residue and aqueous products in moderate to high temperature oxygen deficient environments to obtain high yielding energy conversions. |
|
Continuous hydrotreater reactor system High pressure H2 used to deoxygenate biocrude oil to produce hydrocarbon fuels |
|
QUT Banyo site located in Brisbane has additional thermochemical processing equipment including pyrolysis, antisolvent fractionation and supercritical fluid extraction to enable a wide variety of bioprocessing outcomes.
More information
Find out more about the great work being done at the Mackay Pilot Plant.